Health and Safety
(GRI 403-1; 403-2; 403-3; 403-4; 403-5; 403-6; 403-7; 403-8)
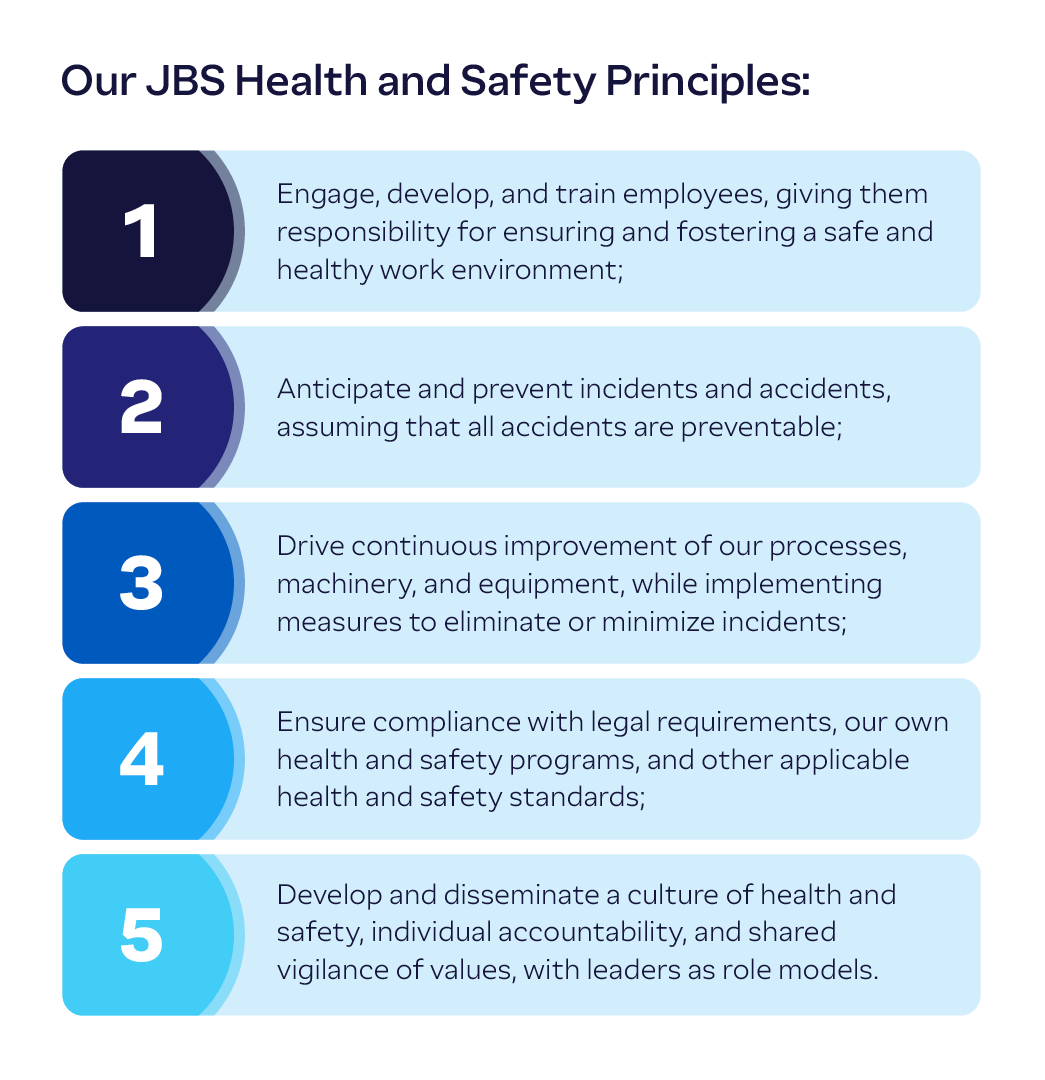
The health and safety of our team members is paramount. We prioritize providing safe working conditions and work environments across all JBS facilities. Our commitment to health and safety begins with our culture of accountability, which empowers each team member to understand and practice health and safety guidelines while remaining vigilant.
We reinforce our culture with frequent training and development around our Code of Conduct and Ethics and Global Health and Safety Policy. Our safety governance structure and management approach are guided by our Global Health and Safety Policy and aligned to the relevant regulatory requirements of each country in which we operate. We follow governing bodies like those listed to evaluate the effectiveness of external safety audit processes, collect feedback, and make necessary adjustments.
JBS Global Health and Management System Coverage
(GRI 403-8)
Workforce Type | Employees |
Covered by a Health and Safety Management System | 100% |
Covered by a Health and Safety Management System that is Internally Audited | 93% |
Covered by a Health and Safety Management System that is Externally Audited or Certified | 15% |
Our safety governance structure and management approach are guided by our Global Workplace Health and Safety Policy and aligned to the relevant regulatory requirements of each country in which we operate. We defer to governing bodies like those listed below to evaluate the effectiveness of external safety audit processes, collect feedback, and make necessary adjustments.
Our Regional Approaches:
Australia:
In Australia, each jurisdiction enforces their own Work Health and Safety Act and regulations, and our facilities comply with them in each region. Our overarching safety management...
Australia:
In Australia, each jurisdiction enforces their own Work Health and Safety Act and regulations, and our facilities comply with them in each region. Our overarching safety management system framework in Australia aligns with the National Audit Tool (NAT) for self-insurers, which is based on the Australian Standard 4804 Occupational Health and Safety Management and Australian Standard 4801 Occupational Health and Safety Management Systems.
Brazil:
In Brazil, occupational health and safety management is in line with the Regulatory Norms (NR) of the Ministry of Labor. In total, there are 37 standards that outline the health...
Brazil:
In Brazil, occupational health and safety management is in line with the Regulatory Norms (NR) of the Ministry of Labor. In total, there are 37 standards that outline the health and safety measures that must be followed by the company.
Canada:
In Canada, our Health and Safety Management System is aligned with the Alberta Occupational Health and Safety (OH&S) law. In addition, our Alberta facility is a holder...
Canada:
In Canada, our Health and Safety Management System is aligned with the Alberta Occupational Health and Safety (OH&S) law. In addition, our Alberta facility is a holder of a Certificate of Recognition (COR) through a certified auditor, Alberta Food Processing Association (AFPA).
Europe:
In Europe, our programs meet the Health Safety Executive RIDDOR (Reporting of Incidents Diseases and Dangerous Occurrences) Regulations.
Mexico:
In Mexico, our team tracks data according to the government Secretaria del Trabajo and the Safety and Health regulations, which comply with OSHA standards.
United States:
Our U.S. and Puerto Rican facilities operate in alignment with U.S. Occupational Safety and Health Administration (OSHA) standards.
Actions to Support Health and Safety
Training and Education
We provide frequent health and safety training to reduce the number of work-related injuries and illnesses throughout our facilities. Our in-depth safety training consists of new team member orientation, job- and task-specific training, departmental safety meetings, and regular refresher training. All newly hired team members must complete classroom and department-specific training, which are made available in multiple languages. In addition, we have implemented a virtual reality technology to train team members on food and team member safety protocol.
Audits
Each year, JBS locations undergo a comprehensive safety management system audit, fleet safety audit, and occupational health audit based on applicable legislation and company procedures. Many facilities also conduct comprehensive safety analysis audits to identify and reduce potential hazards. These audits focus on early detection of risks and in-depth reviews of policies and programs related to preventing electrical safety issues, ergonomics weaknesses, falls and slips, and machine guarding issues.
Corrective Actions
Despite our focus on health and safety training and accident prevention, some incidents do occur, and we must acknowledge, report, and learn from these safety-related incidents. Our facilities have formal incident investigation procedures and/or committees to investigate and reduce, mitigate, and eliminate injuries, illnesses, and fatalities. The incident investigation process assists operations in preventing the recurrence of similar incidents and in identifying injury and illness trends, potential weaknesses or failures in our safety management, and proximate root causes of incidents. This process allows us to develop effective corrective action plans. In addition, within each business unit, locations regularly share incident investigation information to facilitate learning and prevention.
Data-Driven Insights
We have integrated safety data across digital platforms to identify enterprise-wide trends and best practices related to health and safety. Data-driven insights support us to perform root-cause analysis and take corrective actions such as audits and safety inspections. Insights also help us to define best practices that we can share across the organization.
Innovation
We continue to find new ways to leverage cutting-edge technology to enhance team member safety.
Right to Speak Policy
If a team member notices an unsafe act or condition, we empower them to speak up so that we can stop unwanted behavior and restore optimal conditions immediately. We encourage every team member to report without fear of retribution. Our company policy prohibits retaliation, and we emphasize the importance of reporting to the success of our organization. Any incidence of retaliation against an employee for such actions will result in the immediate termination of the person engaging in the retaliation. As a final precaution, we advise team members that they are entitled to remove themselves from any situation they deem to be unsafe.
Safety Goals, Indexing, and Measurement
Annual companywide and facility-specific safety goals help our organization prioritize health and safety, with leading safety indicators reported weekly to all heads of HR, safety, operations, and business unit presidents. Safety issues can encompass a wide range of situations, including drivecam coaching effectiveness, electrical safety, machine guarding, preventable vehicle accidents, safety gaps, and working surfaces. All operational supervisors must conduct multiple safety observations each week and intervene with helpful coaching to prevent an unsafe act, condition, or injury.
Finally, we maintain a Safety Index at each facility to measure the frequency of severe injuries per hour of operation. We define a severe injury as any injury resulting in amputation, fatality, in-patient hospitalization, vision loss, second- or third-degree burns, or fractures that results in greater than fifteen days lost time, and any other injury that results in greater than fifteen days lost time. We have set a goal to collectively improve our Global Safety Index by thirty percent by 2030, compared to a 2019 baseline. In 2023, we achieved a 59% reduction from our baseline.
Despite our robust efforts to provide a safe working environment for all JBS team members, we unfortunately experienced one employee fatality in 2023. In the event a fatal accident such as this occurs, we take immediate action to fully investigate the incident in cooperation with authorities and in accordance with the appropriate regulations and laws for each region. During our evaluation, we seek to understand the circumstances, identify the root cause, and prevent any potential re-occurrence. We also review our safety protocols to determine any gaps and make any necessary improvements such as enhanced procedures or additional training. The safety and well-being of our team members remains our top priority, and we are dedicated to providing safe working conditions for everyone.
Global Safety Performace
(GRI 403-9, SASB FB-MP-320a.1)
2020 | 2021 | 2022 | 2023 | ||
JBS Australia | |||||
Hour Worked | 17,512,099 | 16,552,736 | 20,538,199 | 22,636,657 | |
Safety Index | 0.53 | 0.48 | 0.56 | 0.43 | |
LTIFR | 11.3 | 11.16 | 12.98 | 16.17 | |
Fatalities | 0 | 0 | 0 | 0 | |
JBS Brazil | |||||
Hour Worked | 239,741,327 | 253,431,036 | 262,517,767 | 278,199,801 | |
Safety Index | 0.25 | 0.18 | 0.14 | 0.1 | |
Fatalities | 3 | 6 | 3 | 1 | |
JBS Canada | |||||
Hour Worked | 5,376,010 | 5,611,592 | 5,590,666 | 6,039,631 | |
Safety Index | 0.04 | 0.11 | 0.04 | 0.07 | |
Fatalities | 0 | 0 | 0 | 0 | |
JBS USA & Pilgrim's U.S. | |||||
Hour Worked | 139,378,346 | 139,431,101 | 142,800,620 | 144,339,567 | |
Safety Index | 0.14 | 0.11 | 0.14 | 0.13 | |
DART Rate | 2.49 | 2.63 | 2.32 | 2.95 | |
TRIR | 3.91 | 4.19 | 3.77 | 3.33 | |
Fatalities | 1 | 1 | 2 | 0 | |
Pilgrim's Europe | |||||
Hour Worked | 31,547,831 | 30,355,198 | 38,955,562 | 36,660,759 | |
Safety Index | 0.16 | 0.07 | 0.03 | 0.04 | |
DART Rate | 1.28 | 1.3 | 0.94 | 0.35 | |
Fatalities | 0 | 0 | 0 | 0 | |
Pilgrim's Mexico | |||||
Hour Worked | 26,733,949 | 26,554,735 | 29,320,766 | 30,396,983 | |
Safety Index | 0.02 | 0.02 | 0.02 | 0 | |
DART Rate | 0.04 | 0.04 | 0.04 | 0.04 | |
Fatalities | 0 | 0 | 0 | 0 | |
Rigamonti | |||||
Hour Worked | - | - | - | 626,494 | |
Safety Index | - | - | - | 1.27 | |
Fatalities | - | - | - | 0 | |
Vivera | |||||
Hour Worked | - | - | - | 855,090 | |
Safety Index | - | - | - | 0.47 | |
Fatalities | - | - | - | 0 |
Training and Education
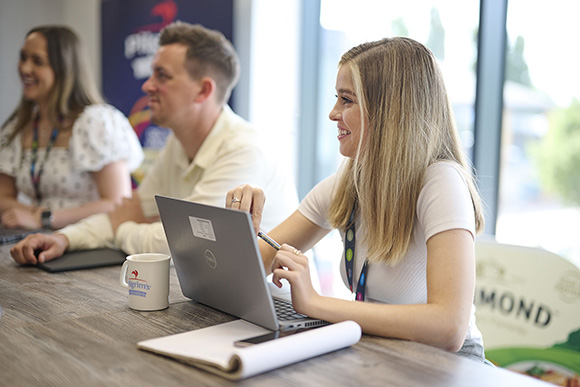
Our Regional Approaches:
Australia:
In Australia, all independent contractors are required to meet the Australian Standard 4804 Occupational Health and Safety Management and the Australian Standard 4801 Occupational Health and Safety Management Systems.
Brazil:
In Brazil, the Code of Conduct for Business Associates, which outlines health and safety guidelines, is attached to all independent contracts. In addition, suppliers ...
Brazil:
In Brazil, the Code of Conduct for Business Associates, which outlines health and safety guidelines, is attached to all independent contracts. In addition, suppliers receive forms containing all applicable security requirements for accessing JBS operational units.
Europe and Mexico:
In Europe and Mexico, all independent contractors are required to meet our health and safety standards.
United States and Canada:
In the U.S. and Canada, contractors are required to have an “A” or “B” grade to work at our facilities, as determined by third-party assessors. Those contractors with “C” and “F” grades must have...
United States and Canada:
In the U.S. and Canada, contractors are required to have an “A” or “B” grade to work at our facilities, as determined by third-party assessors. Those contractors with “C” and “F” grades must have a variance form on file granted by the site Safety and Health Manager and the General Manager. Contractor grades are derived from Contract Safety Information, which includes safety, injury, and illness statistics; aggregate insurance requirements, OSHA inspection history, workers’ compensation experience modifier (EMR), OSHA forms 300 and 300A, written health, safety and environmental programs, safety-training documentation; and safety briefing online training.
Case Studies:
- Skills Management: A training program focused on developing the skills required for team members to perform their jobs safely.
- Security Monitors: On-site champions who verify the correct implementation of procedures, ergonomic exercises, use of personal protective equipment (PPE), and detection of unsafe acts or conditions.
- 5-Minutes Talks: Quick, regular discussions aimed at raising awareness among staff for the safe development of daily tasks.
- Onboarding: Initial training to ensure new staff are competent to carry out their activities safely from the point of orientation through the development of their skills and the formation of their values.