Our Environment
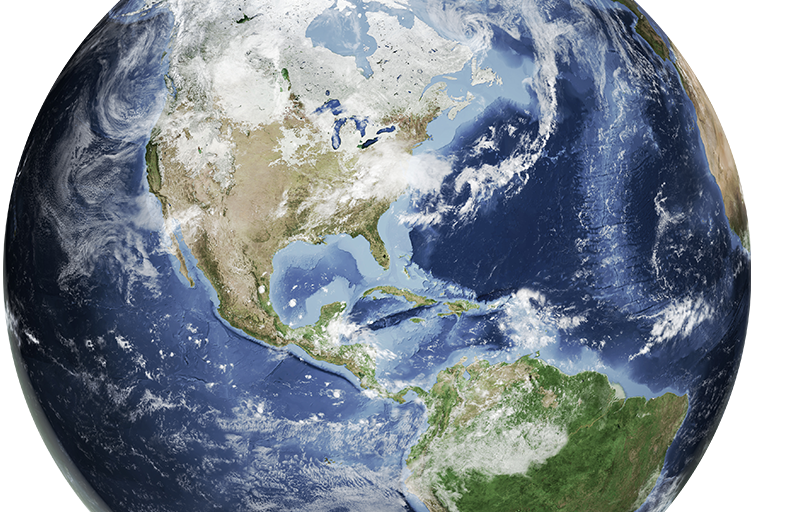
Waste Management
(GRI 306-1; 306-2)
Guided by a Global Packaging and Recycling Policy, our operations around the world work to reduce, reuse or recycle the maximum number of materials and minimize waste to landfills. Opportunities for improved performance in our facilities are identified and addressed in several ways, both daily through site-specific actions and long-term through the development of new technologies for scaled implementation.
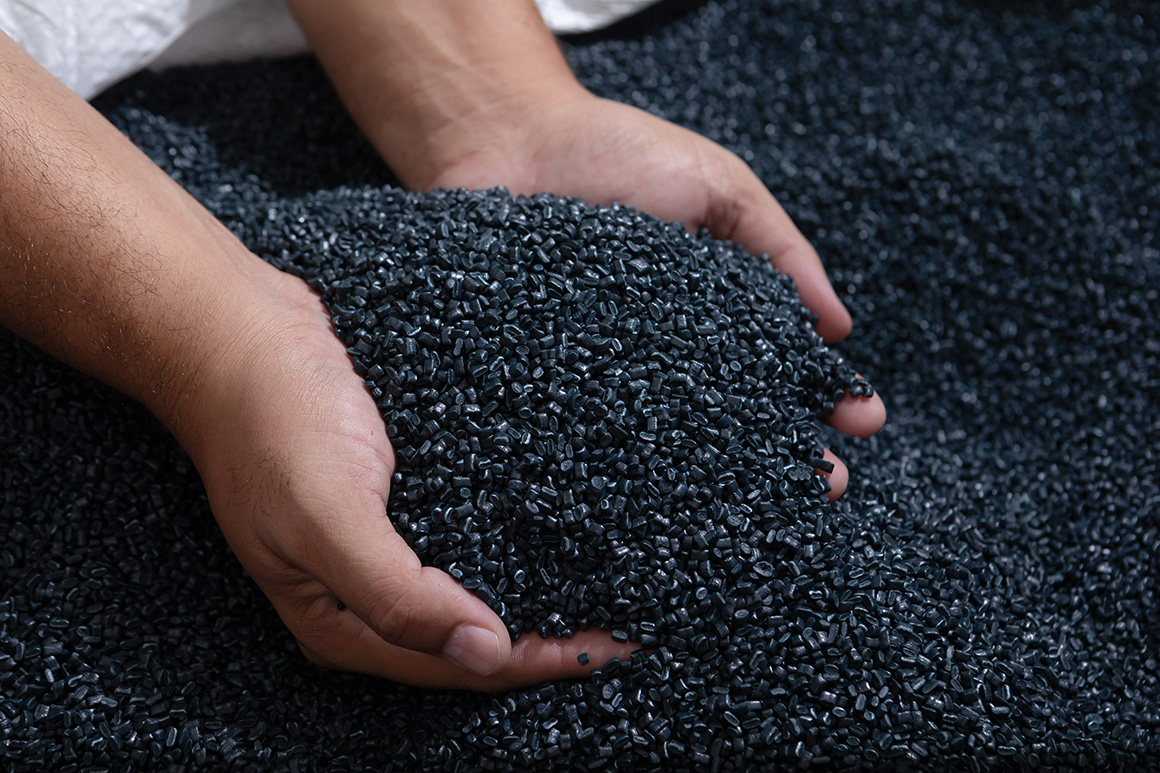
JBS environmental teams outline the appropriate procedures for collecting, transporting, and disposing of waste correctly in accordance with regional laws and regulations, and define best practices for reduction across our production processes. Materials that can be recycled are separated and sent to recycling companies, and where possible, we partner with composting companies to transform organic waste into compost that can be used as fertilizer in crop fields. Nonrecyclable, hazardous, and harmful waste is separated for appropriate final disposal.
In Brazil, our Ambiental business specializes in waste management and plastic recycling. We have waste diversion and minimization initiatives in place at 23 operations across our Friboi, Seara, JBS Couros, and Swift businesses, where the team supports the management of recyclable waste and the segregation, processing, and transformation of plastic into new products through recycling.
Global Waste Generated in Operations by Disposal(GRI 306-3; 306-4; 306-5) |
||||||||||
2023 | 2022 | |||||||||
Hazardous Waste¹ | Non-Hazardous Waste | Total Waste | Hazardous Waste¹ | Non-Hazardous Waste | Total Waste | |||||
MT | % | MT | % | MT | MT | % | MT | % | MT | |
Total Waste Generated | 62,057 | 2% | 3,633,591 | 98% | 3,695,648 | 34,247 | 1% | 2,561,056 | 99% | 2,595,303 |
Waste diverted for final disposal | 12,453 | 0% | 2,887,878 | 100% | 2,900,331 | 25,490 | 1% | 1,893,600 | 99% | 1,919,090 |
Diverted to a 3rd party | 12,453 | 0% | 2,672,391 | 100% | 2,684,844 | 25,490 | 2% | 1,622,708 | 98% | 1,648,198 |
Reuse | 0 | 0% | 0 | 0% | 0 | 0 | 0% | 0 | 0% | 0 |
Recycling | 10,165 | 2% | 604,932 | 98% | 615,097 | 806 | 0% | 248,175 | 100% | 657,504 |
Composting | 0 | 0% | 1,308,460 | 100% | 1,308,460 | 22,414 | 3% | 719,299 | 97% | 741,713 |
Reverse Logistics | 0 | 0% | 0 | 0% | 0 | 0 | 0% | 0 | 0% | 0 |
Other | 2,288 | 0% | 758,999 | 100% | 761,287 | 2,270 | 0% | 655,234 | 100% | 657,504 |
Diverted internally (JBS) | 0 | 0% | 215,487 | 100% | 215,487 | 0 | 0% | 270,892 | 100% | 270,892 |
Reuse | 0 | 0% | 0 | 0% | 0 | 0 | 0% | 0 | 0% | 0 |
Recycling | 0 | 0% | 0 | 0% | 0 | 0 | 0% | 0 | 0% | 0 |
Composting | 0 | 0% | 215,340 | 100% | 215,340 | 0 | 0% | 270,892 | 100% | 270,892 |
Reverse Logistics | 0 | 0% | 0 | 0% | 0 | 0 | 0% | 0 | 0% | 0 |
Other | 0 | 0% | 147 | 100% | 147 | 0 | 0% | 0 | 0% | 0 |
Waste directed to disposal | 49,604 | 6% | 745,713 | 94% | 795,317 | 8,757 | 1% | 667,456 | 99% | 676,213 |
Directed to a 3rd party | 47,781 | 6% | 743,078 | 94% | 790,859 | 6,621 | 1% | 663,183 | 99% | 669,804 |
Incineration (with energy recovery) | 23,542 | 11% | 183,438 | 89% | 206,980 | 788 | 1% | 95,716 | 99% | 96,504 |
Incineration (w/o energy recovery) | 90 | 0% | 21,172 | 100% | 21,262 | 177 | 1% | 17,935 | 99% | 18,112 |
Landfill | 24,088 | 5% | 504,614 | 95% | 528,702 | 5,597 | 1% | 523,595 | 99% | 529,192 |
Other | 61 | 0% | 33,854 | 100% | 33,915 | 59 | 0% | 25,937 | 100% | 25,996 |
Directed internally (JBS) | 1,823 | 41% | 2,635 | 59% | 4,458 | 2,136 | 33% | 4,273 | 67% | 6,409 |
Incineration (with energy recovery) | 0 | 0% | 0 | 0% | 0 | 0 | 0% | 0 | 0% | 0 |
Incineration (w/o energy recovery) | 0 | 0% | 0 | 0% | 0 | 0 | 0% | 0 | 0% | 0 |
Landfill | 1,823 | 41% | 2,635 | 59% | 4,458 | 2,136 | 33% | 4,273 | 67% | 6,409 |
Other | 0 | 0% | 0 | 0% | 0 | 0 | 0% | 0 | 0% | 0 |
Packaging
Proper packaging is essential to keeping our food products safe all the way to the consumer’s table, but it should not come at the expense of our environment. That is why we are continuing to explore alternative materials that offer compliance with regulations and recyclability and technologies that allow us to reduce the amount of packaging needed, while still maintaining strict product safety requirements. One of the aims of our Research and Development (R&D) teams is to reduce and optimize the use of primary (in direct contact with food), secondary, and tertiary packaging, thereby diminishing the amount of waste generated by customers and consumers.
Global Packaging Used (MT)(GRI 301-1; 301-2) |
||||||||
2023 | ||||||||
Total Packaging | 700,891.65 | |||||||
Recyclable Packaging¹ | 280,231.04 | |||||||
Non-Recyclable Packaging | 420,660.61 | |||||||
Recycled Packaging² | 17,316.27 | |||||||
Non-Recycled Packaging | 425,235.05 | |||||||
Renewable Raw Material Packaging³ | 202,179.58 | |||||||
Non-Renewable Raw Material Packaging4 | 486,305.60 | |||||||
Packaging Recovered and Reused Through Reverse Logistics Programs⁵ | 81,909.30 | |||||||
Packaging Not Recovered and Reused Through Reverse Logistics Programs⁵ | 618,982.35 |
- Has the potential for post-consumer recyclability.
- Produced from recycled materials.
- Includes paper, cardboard, pulp, and wood.
- Includes plastic, metal, Styrofoam, and glass.
- Excludes recalled and/or rejected product.
Case Studies:
- Target 1 - Eliminate problematic or unnecessary single-use plastic packaging through redesign, innovation or alternative (re-use) delivery models;
- Target 2 - 100% of plastic packaging to be reusable, recyclable or compostable;
- Target 3 - 70% of plastic packaging effectively recycled or composted;
- Target 4 - 30% average recycled content across all plastic packaging; and All targets to be achieved by 2025.
- Across our Richmond fresh pork sausages, we reduced the thickness of the plastic layer and reduced the bag sizes, resulting in a reduction of 36.1 MT.
- We moved our Richmond frozen sausages from a mixed laminate to mono laminate and reduced bag size, resulting in a reduction of 49 MT and increasing the recyclability of our packaging.
- Across our chilled ready meals, we introduced a pulp tray for one of our customers, removing 205 MT of virgin plastic annually.
- For another customer, we moved from 2 x virgin plastic PP trays to a single A-pet clam shell designed with recycled plastic, reducing 20 MT of plastic waste.
- At our Carrickmacross site, we have removed another 17 MT of plastic by removing all plastic tape from site.